1、酸性水的來源:
石油及其產品中存在含硫化合物和含氮化合物, 在常減壓、催化裂化、延遲焦化、催化加氫等加工過程中, 這些化合物會通過高溫裂解、催化裂化、加氫裂化等反應生成H2S和NH3-N而進入產品物流中,這些產品物流經過冷凝脫水或水洗處理, 即產生含硫含氨廢水, 俗稱含硫廢水或酸性水。
2、酸性水特點及危害:
焦粉含量高,且粒徑分布小,含油量高,油滴粒徑小,且乳化嚴重;大量乳化油和懸浮物(焦粉),影響汽提效果和液氨質量。
容易造成汽提塔堵塞,嚴重時造成非計劃性停產,造成較大損失。
成分復雜且含量波動較大
含硫化物、氨氮等刺激性氣味外泄,嚴重影響影響環境和員工健康。
直接排入污水處理廠,給企業造成巨大環保壓力。
3、酸性水處理傳統工藝及處理難點:
1)重力沉降工藝處理酸性水:目前國內大多數煉化廠采用重力沉降法,沉降時間在50~70小時。由于酸性水含油乳化嚴重,焦粉顆粒小,即使長時間沉降,分離效果仍然不明顯。大罐處于敞開或者半封閉狀態,酸性氣體外泄,嚴重影響周圍環境和員工健康。占地面積大,基建成本高,投資大。全手動,無法自動控制,清理和檢修全靠人力,費時費力。
2)旋流除油除焦粉工藝處理酸性水:部分煉化廠嘗試采用罐中罐旋流以及兩級旋流除焦粉和除油工藝,仍無法根本解決除油除焦粉的問題。雖然較重力沉降有改進,但由于乳化油粒徑小,密度與水相當,旋流作用仍然很有限,除油、除焦粉效果仍不明顯??箾_擊性能差,除油效果不穩定,無法滿足酸性水含油含焦粉波動大的要求。旋流器容易堵塞,嚴重時甚至造成無法正常工作。需要壓力較高,提升泵等功耗大,運行成本高。
3)氣浮+無機陶瓷膜工藝處理酸性水:該工藝,膜過濾精度高,出水比較好,短期內能達到要求。但穩定性較差,沖擊工況,膜容易堵塞,處理量下降,產水率低,產生大量濃水和酸洗、堿洗產生廢液,后續處理困難。壓力高,能耗大,運行成本高。投資高,運行和維護成本高。
4、科力邇科技酸性水處理解決方案:
我司采用CDFU+SiC過濾器+KHC聚結除油器可實現酸性水的油水分離
該技術特點如下:

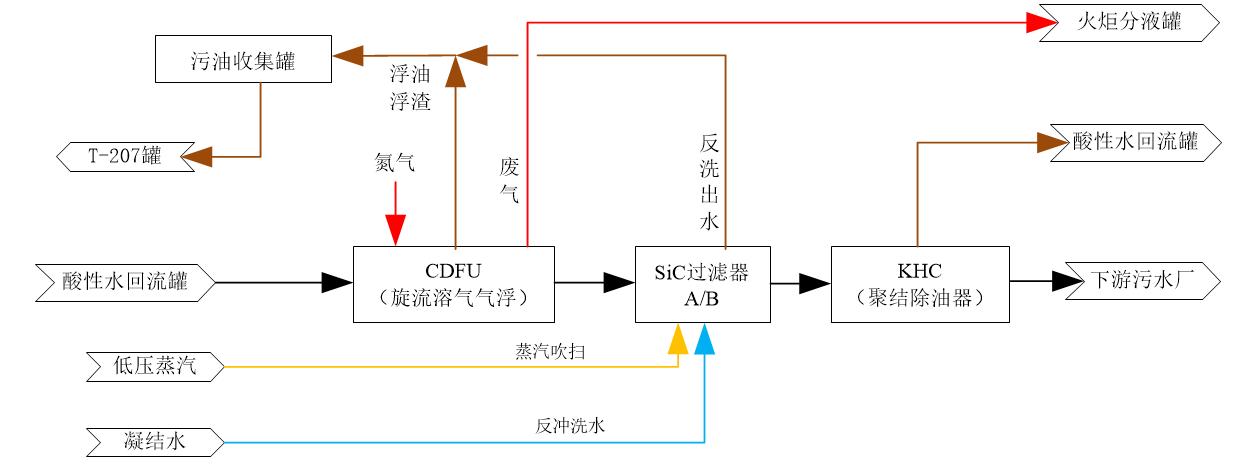
工藝流程圖
5、酸性水處理工藝技術介紹:
酸性廢水進入CDFU,在旋流的作用下,浮油、分散油、乳化油和懸浮物快速與溶氣產生的微納米氣泡迅速碰撞、粘附,被微納米氣泡粘附后的乳化油和懸浮物,由于微納米氣泡表面張力等作用,乳化油膜逐步破裂實現純物理破乳,懸浮物表面污油被微納米氣泡吸附,破乳后的油、懸浮物、微氣泡多相混合物在CDFU中間集聚并上浮到罐體上部進入內部集油筒,通過自壓經排油口排出,處理后出水通過提升泵進入SiC過濾器,其出水懸浮物絕對粒徑可以達到10μm,分離后污油水通過自壓經排油口排出進入污油收集罐,污油收集罐通過污油提升泵將污油打入污油罐中;CDFU排出的廢氣進入火炬分液系統。
CDFU出水經過提升泵后進入SiC過濾器,污水從SiC濾芯中間進四周出,將懸浮物、膠質團等攔截,出水懸浮物絕對粒徑可以達到1μm,過濾器出水進入聚結除油器;過濾器系統壓差較大時需要進行反沖洗,將濾芯上的雜質、油污沖洗干凈避免濾芯堵塞,反沖洗廢水排入污油收集罐中。
酸性廢水進入聚結除油器,除油器通過特殊聚結材料,將小油滴聚結成大油滴進行物理破乳,破乳后由于密度差,油層與水層分離,污油從頂部油包處排出,其含水率小于10%,廢水則從底部排水口排出,從而實現油水分離,出水中含油量小于50ppm(不含溶解油)。
CDFU、SiC過濾器、聚結除油器出水、排油、排渣、排氣和補氣采用全自動控制,溶氣系統進氣量采用自動控制。
此工藝為全自動、密閉帶壓運行,廢氣進火炬分液系統,無安全環保風險。
6、該酸性水處理工藝進、出水指標:
項目 | 技術指標 | |
石油類 | 懸浮物 | |
工藝進水 | <10000mg/L | <1000mg/L |
工藝出水 | <10mg/L(不計溶解油) | <20mg/L |
7、案例展示:
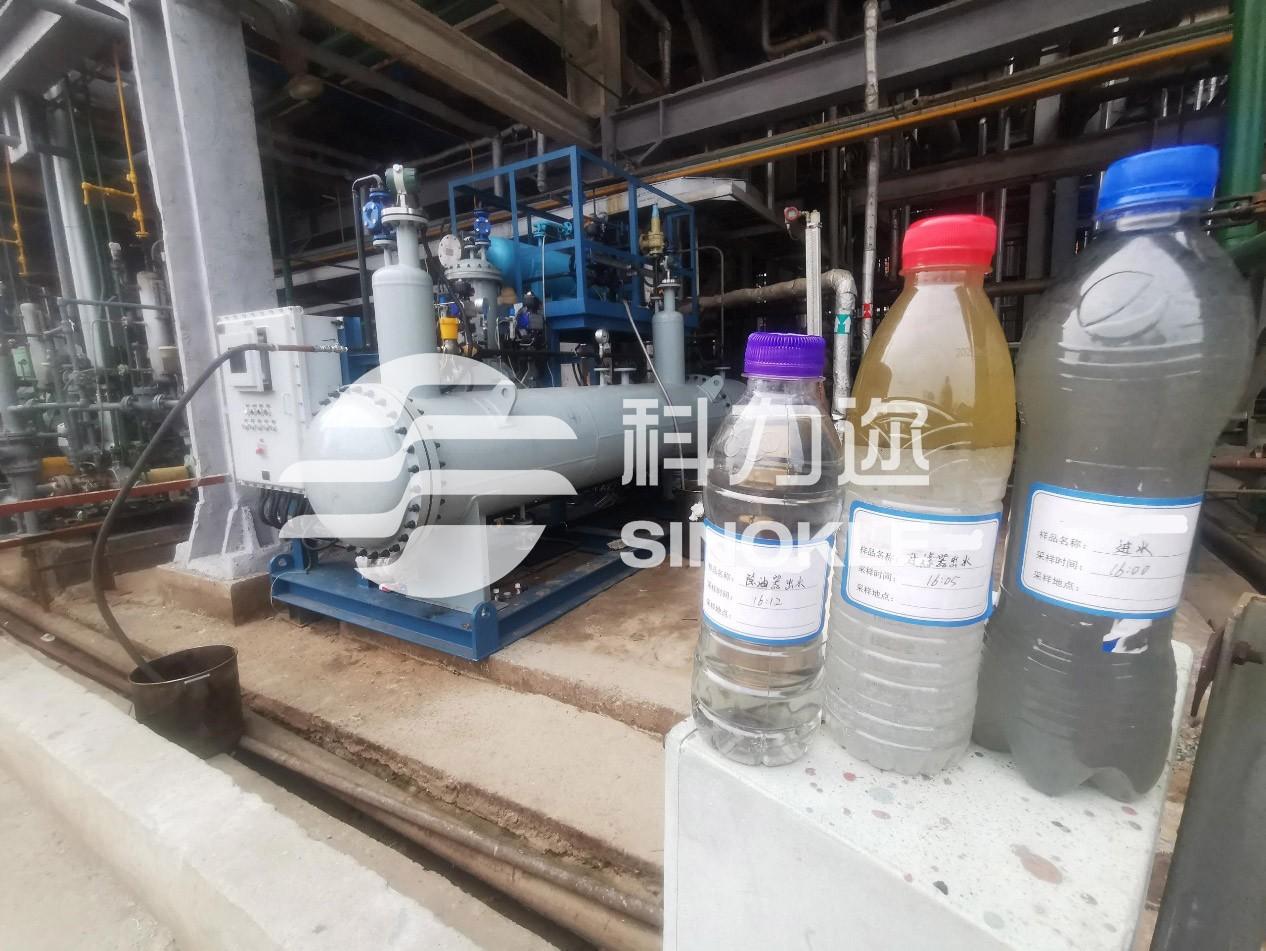